Haben Sie ein Metallspritzguss-Projekt, bei dem wir Ihnen helfen können?
Fallstudie 1
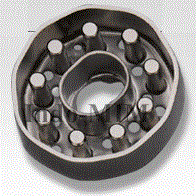
Der Hintergrund
Ein Hersteller wollte von Indo-MIM ein magnetisches und hochkorrosionsbeständiges Material (MIM Fe3%Si) mit den Abmessungen 10mm x 28mm x 31mm und einem Gewicht von 17 Gramm haben. Für diesen Hersteller lieferte Indo-MIM die perfekte Lösung.
Das Problem
Das benötigte Material war in geschmiedeter Form nicht verfügbar. Das Material musste hochgradig magnetisch und korrosionsbeständig sein, und daher musste das Teil verschiedene Prozesse durchlaufen. Zunächst musste es gestanzt werden, dann wurden die magnetischen Stifte an ein nichtmagnetisches, rundes Blech geschweißt, das dann elektrolytisch vernickelt werden musste. All diese Verfahren erhöhten die Herstellungskosten und minderten die Qualität des Bauteils. Die Rechtwinkligkeit der Stifte ließ sich nur schwer beibehalten, da die Stifte auf das Blech geschweißt wurden.
Die Lösung
INDO-MIM war der beste Ort für den oben genannten Hersteller. Die Anforderung bestand in engen Toleranzen, was ein Spezialgebiet von Indo-MIM war. So entwickelte Indo-MIM ein maßgeschneidertes Magnetmaterial für das Produkt gemäß den Spezifikationen des Herstellers. Der Kern und der Hohlraum im Werkzeug nahmen die neun Stifte auf, wodurch die Schweiß- und Stanzarbeiten zur Verstärkung des Endprodukts entfallen konnten.
INDO-MIM entwickelte auch ein Multi-Cavity-Werkzeug, das dazu beitrug, die hohen Volumenanforderungen des Herstellers zu erfüllen.
Fallstudie 2
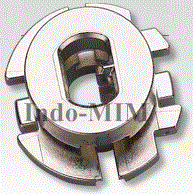
Der Hintergrund
INDO-MIM hat unsere Fähigkeiten auch im Fertigungssektor unter Beweis gestellt. Für einen unserer renommierten Kunden, der Schlösser herstellt, bot Indo-MIM eine innovative Lösung an. Der Schlosshersteller benötigte einsatzgehärteten Stahl (MIM 8620) für ein Schloss mit den Abmessungen 23 mm x 23 mm x 13,5 mm und einem Gewicht von 14,5 g. Indo-MIM lieferte die perfekte Lösung.
Das Problem
Der Hersteller hatte Schwierigkeiten mit mehrstufigen Bearbeitungsvorgängen. Außerdem hatte der Hersteller Schwierigkeiten bei der Bearbeitung von komplexen 3D-Merkmalen wie Schlitzen, Nuten und Löchern, für die der Hersteller versucht hatte, in Guss zu investieren, aber die Anforderungen an die Oberflächengüte konnnten nicht erfüllt werden. Daher musste der Hersteller eine maschinelle Bearbeitung durchführen, um seine kritischen Toleranzen einzuhalten. Die bei der Bearbeitung entstehenden Grate beeinträchtigten die Funktionalität des Teils, und sowohl die Bearbeitung als auch der Feinguss konnten die wachsenden Anforderungen des Kunden nicht erfüllen.
Die Lösung
INDO-MIM hat sich zu einer innovativen Technologieressource für Teile mit 3D-Komplexität entwickelt. Das Unternehmen hat einfache, aber sehr effektive Lösungen für unsere geschätzten Kunden entwickelt. Das einsatzgehärtete Metallspritzgussmaterial von Indo-MIM war problemlos in der Lage, die Materialanforderungen und die mechanischen Eigenschaften zu erfüllen, die der Kunde für seine Produkte benötigte. INDO-MIM hat speziell ein Metallspritzgusswerkzeug mit 2 Einsätzen und 4 Schiebern entwickelt. Darüber hinaus konnte INDO-MIM auch alle Nachbearbeitungen nach dem Metallspritzgussverfahren für Merkmale wie Nuten, Schlitze und Löcher ohne Grate vermeiden. Das Ergebnis war ein zufriedener Kunde, der 30 % der Gesamtkosten für das Projekt einsparen konnte.
Fallstudie 3
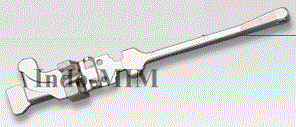
Der Hintergrund
Das Engagement von INDO-MIM, die beste Lösung zu liefern und kontinuierlich Innovationen voranzutreiben, zeigt sich hier einmal mehr. Ein Hersteller stand vor einer Herausforderung mit seiner hochmodernen Bildverarbeitungsanwendung. Der Hersteller benötigte ein Teil aus Edelstahl (MIM 17-4PH) für seine endoskopischen Anwendungen, das 29,34 Gramm wog und die Maße 115 mm x 15 mm x 22 mm hatte.
Das Problem
Der Hersteller hatte Schwierigkeiten, kritische Merkmale wie Schlitze, Löcher, Oberflächen und Vorsprünge zu bearbeiten. Der Hersteller erkannte, dass das Feingussverfahren nicht in der Lage war, das Werkzeug so zu bauen, dass es alle kritischen Merkmale aufnehmen konnte. Der Hersteller benötigte außerdem eine gute Oberflächengüte mit einem Ra-Wert von 1,2 Mikrometern und Gewinden in einem Winkel durch Metallspritzgusseinsätze. Außerdem hatte der Hersteller mit Verformungen während der Bearbeitung und Wärmebehandlung zu kämpfen.
Die Lösung
INDO-MIM fertigte das benötigte Teil mit MIM 17-4 PH, einem hoch korrosionsbeständigen Material. Außerdem wurde das Teil elektropoliert, um das Aussehen der Oberfläche und die Korrosionsbeständigkeit zu verbessern. Die geniale Lösung von INDO-MIM führte zu einer Reduzierung des Gesamtgewichts der Plattform, und das MIM-Werkzeug nahm alle kritischen Merkmale auf, einschließlich der durch das MIM-Werkzeug mit Gewindeeinsätzen hergestellten Gewinde.