Metallspritzgussverfahren (MIM)
Was ist Metallspritzguss?
Der Metallspritzgussverfahren(MIM) kombiniert die Designflexibilität des Kunststoffspritzgusses mit der Festigkeit und Integrität von Knetmetallen und bietet so kostengünstige Lösungen für hochkomplexe Teilegeometrien.
Der Metallspritzgussverfahren besteht in der Regel aus vier einzelnen Verarbeitungsschritten (Compoundieren, Gießen, Entbinden und Sintern) zur Herstellung eines endgültigen Teils.
Prozessschritte des Metallspritzguss:
- Compoundieren
- Gießen
- Entbindern
- Sintern
- Compoundierung / Rohstoff
![[:en]Compound process[:zh]feed-1[:tr]feed-1[:]](https://mim.weboptify.com/wp-content/uploads/2019/02/feed-1-400x250.jpg)
Compoundierung:
Der Metallspritzgussverfahren beginnt mit dem Compoundierung oder der Aufbereitung des Rohstoffes. Feines Metallpulver mit einer Partikelgröße von weniger als 20µ wird mit thermoplastischen Bindemitteln und Wachsbindemitteln in genauen Mengen gemischt. Das Verhältnis von Metallpulver zu Bindemittel beträgt etwa 60:40 nach Volumen. Die Mischung wird in eine spezielle Mischanlage gegeben und auf eine Temperatur erhitzt, die die Bindemittel zum Schmelzen bringt. Die Masse wird mechanisch gemischt, bis die Metallpulverpartikel gleichmäßig mit den Bindemitteln überzogen sind. Die Masse wird abgekühlt und dann zu frei fließenden Pellets (Rohstoff) granuliert, die von der Metallspritzgießmaschine angenommen werden können.
2. Spritzguss
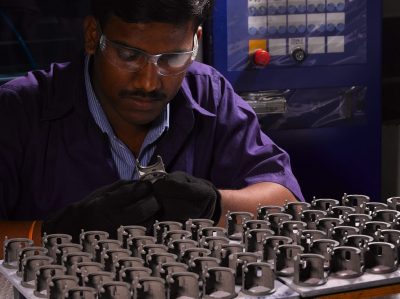
Gießen:
Das Spritzgießen ist in Ausrüstung und Technik identisch mit dem Kunststoffspritzguss. Das pelletierte Rohsteoff wird in eine Spritzgießmaschine eingespeist, wo es erhitzt und unter hohem Druck in einen Formhohlraum gespritzt wird. Das geformte Teil (jetzt als „Grünteil“ bezeichnet) wird abgekühlt und dann aus der Form entnommen, damit der Prozess wiederholt werden kann. Da nur die Bindemittel schmelzen (die die Metallpulver tragen), findet der gesamte Prozess bei etwa 200° C statt. Der Formhohlraum wird um etwa 20 % vergrößert, um die beim Sintern auftretende Schrumpfung zu kompensieren. Die Schrumpfungsänderung ist für jedes Material genau bekannt.
3. Verfahren der Entfernung von Bindemitteln (Entbinderung)
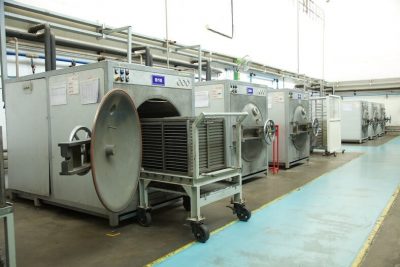
Entbindern:
Nach dem Spritzgießen wird das Formteil zum nächsten Schritt, dem Entbindern oder Entbinderungsprozess, gebracht. Beim Entbindern werden die Bindemittel aus dem geformten MIM-Bauteil entfernt. Dieser Prozess erfolgt in der Regel in mehreren Schritten, wobei der größte Teil vor dem Sinterschritt entfernt wird und nur so viel Binder zurückbleibt, dass die Teile in den Sinterofen gelangen können. Die Entfernung des Binders kann durch verschiedene Methoden erfolgen, wobei die gängigste die Lösungsmittelextraktion ist. Nach der Binderentfernung ist das Teil nun halbporös, so dass der verbleibende Binder während des Sinterprozesses leicht entweichen kann.
4. Sinterverfahren – Sinterteile

Sintern:
Die entbinderten Teile werden auf keramische Abziehbilder gelegt, die in einen Hochtemperatur-Sinterofen mit kontrollierter Atmosphäre geladen werden. Die braunen Teile werden in einer Schutzatmosphäre langsam erhitzt, um die restlichen Bindemittel auszutreiben. Sobald die Bindemittel verdampft sind, wird das Metallteil auf eine hohe Temperatur erhitzt, bei der der Hohlraum zwischen den Partikeln beseitigt wird, da die Partikel miteinander verschmelzen. Das Teil schrumpft isotrop auf seine Konstruktionsmaße und verwandelt sich in einen dichten Festkörper. Die Dichte des Sinterteils liegt bei den meisten Werkstoffen bei über 97 % der theoretischen Dichte. Die hohe Sinterteildichte verleiht dem Produkt Eigenschaften, die denen von Knetwerkstoffen ähnlich sind.
5. Finishing / Secondary Processes
![[:en]Metal Injection Molding MIM materials group 2[:zh]final-group[:tr]final-group[:]](https://mim.weboptify.com/wp-content/uploads/2019/05/final-group-400x213.jpg)
Finishing:
Finishing/Machining processes are not part of the Metal Injection Molding Process. Depending upon final requirements, certain finishing/machining operations may be performed to the sintered part. To improve physical properties, heat treatment can be done as on any metal. Any type of machining operation can be performed to achieve Metal Injection Molding (MIM) tolerances that are more precise than what the process can capably supply. Plating and Coatings can be readily applied due to high material density. Numerous mechanical assembly techniques such as welding or cold working can also be successfully used.