Processo de moldagem por injeção de metal
O processo de MIM combina a flexibilidade de projeto da moldagem por injeção de plásticos com a resistência e integridade de metais forjados para oferecer soluções econômicas para geometrias de peças de alta complexidade. O processo de MIM normalmente é explicado como quatro etapas específicas de processamento (mistura, moldagem, extração e sinterização) para produzir uma peça final que pode ou não precisar de operações de acabamento final.
- Mistura
![[:en]Compound process[:zh]feed-1[:tr]feed-1[:]](https://mim.weboptify.com/wp-content/uploads/2019/02/feed-1-600x375.jpg)
Um pó metálico fino com tamanho de partícula inferior a 20µ é misturado com aglutinantes de cera e termoplásticos em quantidades precisas. A relação entre pó metálico e aglutinante é de aproximadamente 60:40 em volume. A mistura é colocada em um equipamento de mistura especial e aquecida a uma temperatura que ocasiona a fusão dos aglutinantes. A massa é misturada mecanicamente até que as partículas do pó metálico estejam uniformemente revestidas com os aglutinantes. A massa, então, é resfriada e granulada em pellets de fluxo livre (feedstock), que serão aceitos pela máquina de moldagem por injeção.
2. Moldagem por injeção
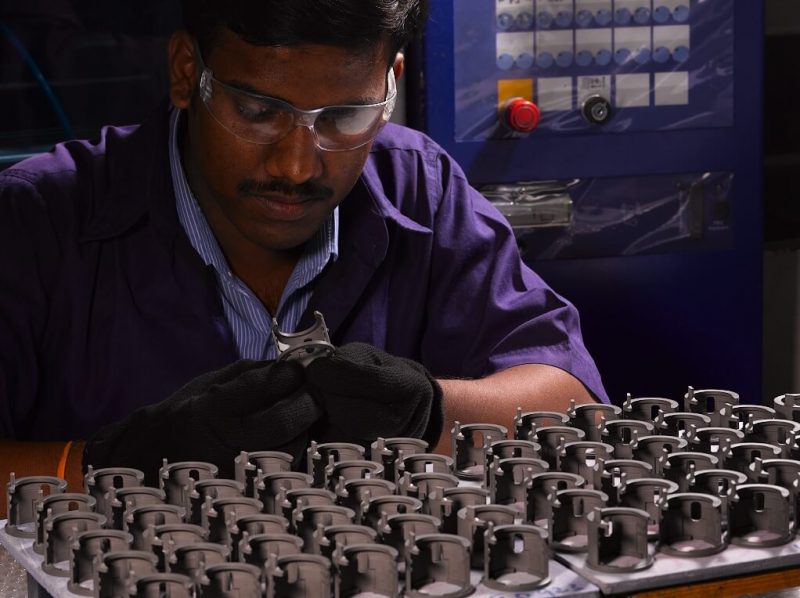
A técnica e o equipamento da moldagem por injeção são idênticos aos da moldagem por injeção de plásticos. A carga injetável peletizada (feedstock) é alimentada em uma máquina onde é aquecida e injetada em um molde sob alta pressão. Ao esfriar, a peça (agora denominada “verde”) é ejetada do molde para que o processo possa ser repetido. Como somente os aglutinantes derretem (para carregar os pós metálicos), todo o processo acontece a cerca de 200°C. O ferramental pode ser de moldes múltiplos para altas taxas de produção. O tamanho do molde é aproximadamente 20% maior para compensar a contração que ocorre durante a sinterização. A alteração da contração é conhecida de forma precisa para cada material.
3. Extração
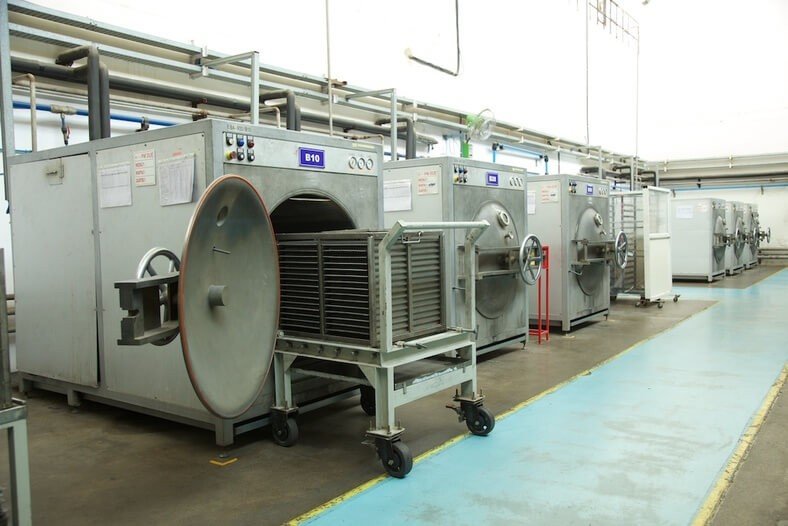
A extração é o processo no qual os aglutinantes são removidos do componente moldado. Esse processo normalmente é realizado em várias etapas nas quais a maior parte dos aglutinantes é removida antes da etapa da sinterização, deixando apenas aglutinante suficiente para poder transferir as peças para o forno de sinterização. A extração pode ser realizada por vários métodos, dos quais o mais utilizado é a extração por solvente. Após a extração, a peça apresenta um aspecto semiporoso, o que permite que o aglutinante remanescente escape facilmente durante a sinterização.
4. Sinterização
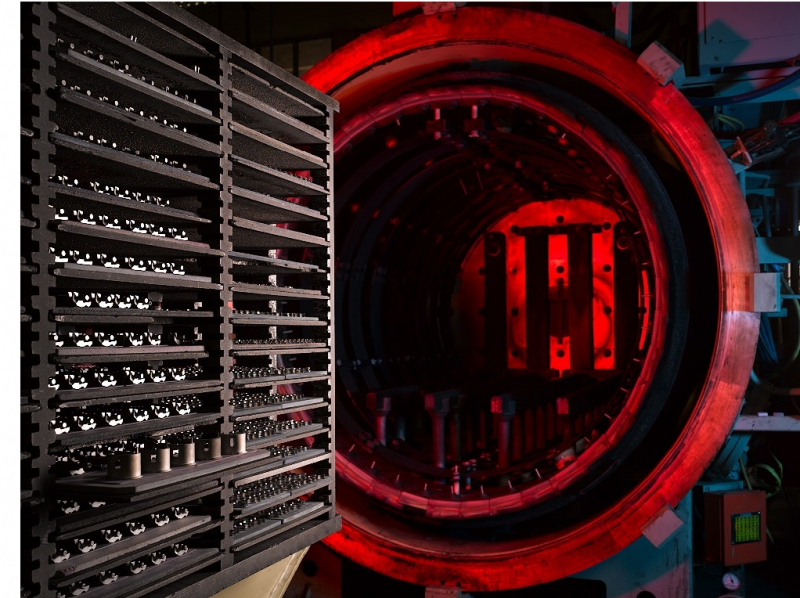
As peças fabricadas são colocadas em moldes de cerâmica que são inseridos em um forno de alta temperatura e atmosfera controlada. As peças são aquecidas lentamente em uma atmosfera protetora para liberar os aglutinantes remanescentes. Uma vez evaporados os aglutinantes, a peça é aquecida a uma alta temperatura com a qual o espaço vazio entre as partículas é eliminado à medida que as partículas se fundem. A peça se contrai isotropicamente para as suas dimensões de projeto e se transforma em um sólido denso. A densidade sinterizada é, normalmente, maior do que a densidade teórica de 97% para a maioria dos materiais. A alta densidade sinterizada confere ao produto propriedades similares às dos produtos forjados.
5. Acabamento
![[:en]Metal Injection Molding MIM materials group 2[:zh]final-group[:tr]final-group[:]](https://mim.weboptify.com/wp-content/uploads/2019/05/final-group.jpg)
Dependendo dos requisitos finais, certas operações de acabamento podem ser realizadas na peça sinterizada. Para melhorar as propriedades físicas, o tratamento térmico pode ser efetuado como em qualquer outro metal. Podem ser realizados quaisquer tipos de operação de usinagem para alcançar tolerâncias que sejam mais precisas do que as que o processo tem capacidade de fornecer. Revestimentos e metalização podem ser prontamente aplicados devido à elevada densidade do material. Várias técnicas de montagem mecânica, como soldagem ou trabalho a frio, também podem ser usadas com sucesso.