금속 사출 성형 공정
금속 사출 성형 공정은 플라스틱 사출 성형의 설계 유연성과 단조 금속의 강도 및 무결성을 결합하여 매우 복잡한 부품 형상을위한 비용 효율적인 솔루션을 제공합니다.
금속 사출 성형 공정은 일반적으로 최종 부품을 생산하기 위한 네 가지 고유한 공정 단계(혼합, 사출, 탈지, 및 소결)로 설명됩니다.
- 혼합 / 공급원료
![[:en]Compound process[:zh]feed-1[:tr]feed-1[:]](https://mim.weboptify.com/wp-content/uploads/2019/02/feed-1-600x375.jpg)
금속 사출 성형(MIM) 공정은 혼합 또는 공급 원료 준비 공정에서 시작됩니다. 20μ 미만의 미세 금속 분말은 열가소성 수지 및 왁스 바인더와 정밀한 양으로 혼합됩니다. 금속 분말 대 바인더 비율은 부피 기준으로 약 60:40입니다. 혼합물을 특수한 혼합 장비에 넣고 혼합물이 녹는 온도까지 가열합니다. 금속 분말 입자가 바이인더와 균일하게 코팅 될 때까지 혼합물 덩어리를 기계적으로 혼합합니다. 혼합물 덩어리는 냉각 된 다음 금속 사출 성형기에 투입될 수 있는 수준의 자유 유동 펠릿 (공급 원료)으로 과립화됩니다.
2.사출성형
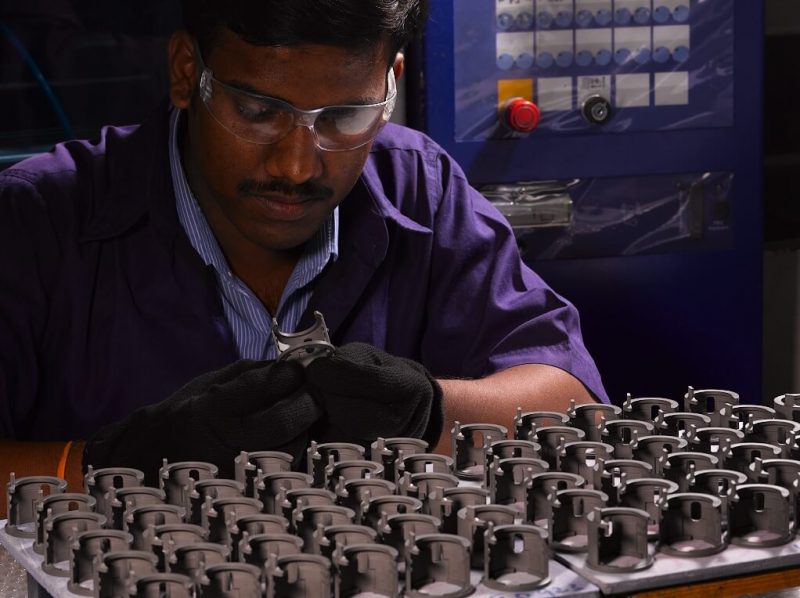
사출 성형은 플라스틱 사출 성형 방법과 장비 및 기술면에서 동일합니다. 펠릿화 된 공급 원료는 사출 성형기에 공급되어 고압 하에서 가열되고 금형 캐비티에 주입됩니다. 사출 성형 된 부품 (현재 “녹색 부품”이라고 함)은 냉각 후, 금형에서 배출되며 이 공정은 반복 될 수 있습니다. 바인더만 녹기 때문에 (금속 분말을 운반하기 위한), 전체 공정은 약 200 ° C에서 발생합니다. 금형은 높은 생산성을 위해 여러 캐비티로 만들어 질 수 있습니다. 금형 캐비티는 소결 중에 발생하는 수축을 보상하기 위해 약 20% 더 큽합니다. 수축 변형은 각 재질에 대해 정확하게 알려져 있습니다.
3.바인더 제거 (탈지) 공정
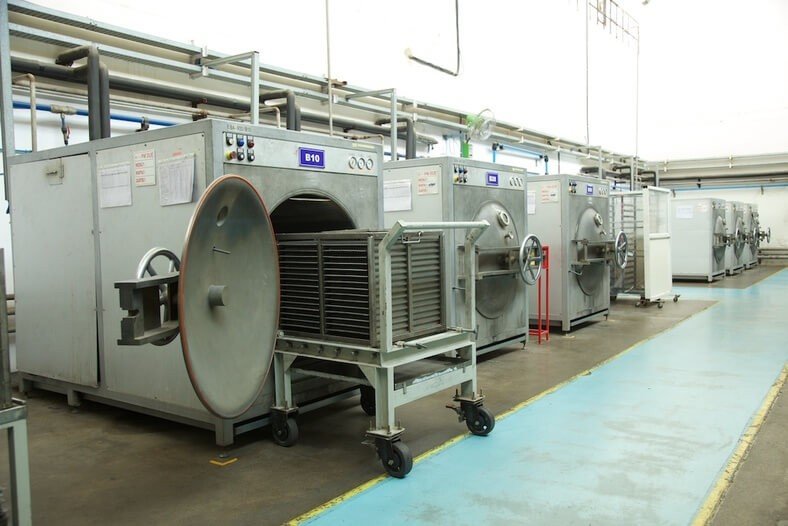
사출 성형 후, 사출 성형품은 탈지 또는 바인더 제거 공정이라 불리는 다음 단계로 이동합니다. 바인더 제거는 바인더 재질이 성형된 MIM 부품에서 제거되는 공정입니다. 이 공정은 일반적으로 소결 단계 전에 바인더 대부분이 제거되어 부품이 소결로에서 처리 될 수 있는 수준의 바인더만 남도록 여러 단계로 진행됩니다. 바인더 제거는 여러 방법으로 수행 할 수 있으며, 가장 널리 사용되는 방법은 용매 추출입니다. 바인더 제거 후 부품은 이제 반 다공성이되어 남아있는 바인더가 소결 과정에서 쉽게 빠져 나갈 수 있습니다.
4.소결 고정 – 소결품
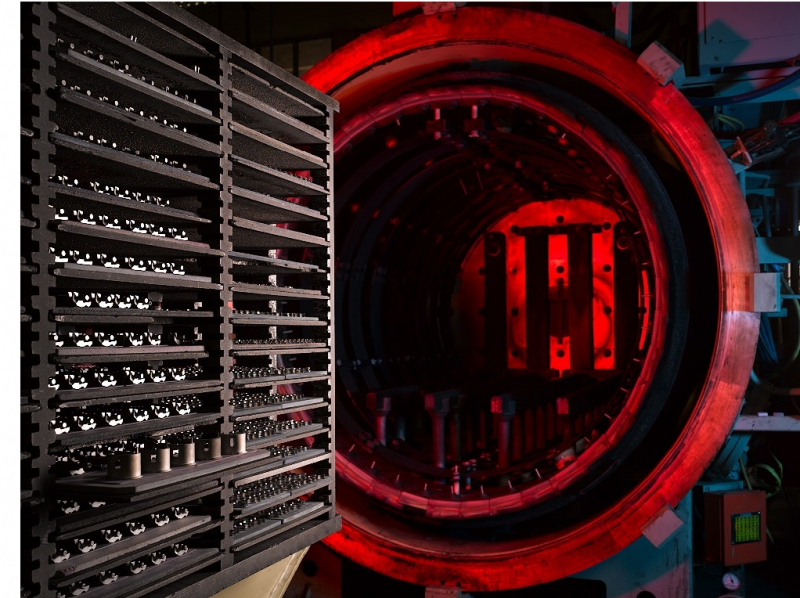
탈지품은 고온, 가스 제어 소결로에 장입되는 세라믹 판에 배열됩니다. 탈지품은 분위기에서 천천히 가열되어 나머지 바인더를 제거합니다. 바인더가 증발하면 금속 부품이 등방성고온으로 가열되어 입자가 융합됨에 따라 입자 사이의 빈 공간이 제거됩니다. 부품은 등방성으로 설계 치수로 축소되고 조밀한 고체로 변형됩니다. 소결품의 밀도는 일반적으로 대부분의 재료에서 이론상의 97% 보다 높습니다. 높은 소결 부품 밀도는 단조물과 유사한 제품 특성을 제공합니다
5.마감 / 후공정
![[:en]Metal Injection Molding MIM materials group 2[:zh]final-group[:tr]final-group[:]](https://mim.weboptify.com/wp-content/uploads/2019/05/final-group.jpg)
마감/가공 공정은 금속 사출 성형 공정의 일부가 아닙니다. 최종 요구 사항에 따라 특정 마감/가공 작업이 소결품에 추가로 수행될 수 있습니다. 물리적 특성을 향상시키기 위해 여타 금속과 마찬가지로 열처리를 할 수 있습니다. MIM 공정에서 맞출 수 있는 공차보다 더 정확한 금속 사출 성형의 공차를 달성하기 위해 모든 유형의 가공 작업을 수행 할 수 있습니다. 도금 및 코팅은 높은 원자재 밀도로 인해 쉽게 적용 할 수 있습니다. 용접이나 냉간가공과 같은 다양한 기구 조립 기술도 성공적으로 사용할 수 있습니다.