From Metal Powders to Complex Components- Innovation in 3D Printing
One of the world’s leading metal injection molding manufacturers, INDO-MIM, has branched out into the production of spherical gas atomized powders and as well as contract manufacturing of metal components through 3D Printing or Additive manufacturing (AM). Having a world-class gas atomized metal powder manufacturing facility in Bengaluru, India.
INDO-MIM has established a melting capacity of ~1100 tons/annum producing highly spherical powders for Metal injection molding (MIM), Laser powder bed fusion (LPBF) and Binder jet metal printing (BJT) technologies. A wide range of metal powders with particle size distribution ranging from 5-150 µm are being produced for a broader range of AM applications. Material portfolios include Stainless steels, Tool steels, ferrous, Nickel, and Cobalt-based superalloys. Powders with custom particle size distribution (PSD) and/or chemistry can be door delivered at a competitive price and the shortest lead time
INDO-MIM’s specialty engineered metal powders with optimum particle size distribution (PSD), and flowability enable printing components with highest print quality eliminating unwarranted secondary finishing operations post sintering. Thanks to proprietary anti-satellite system ensuring powder with no satellite formation resulting in high quality printed components.
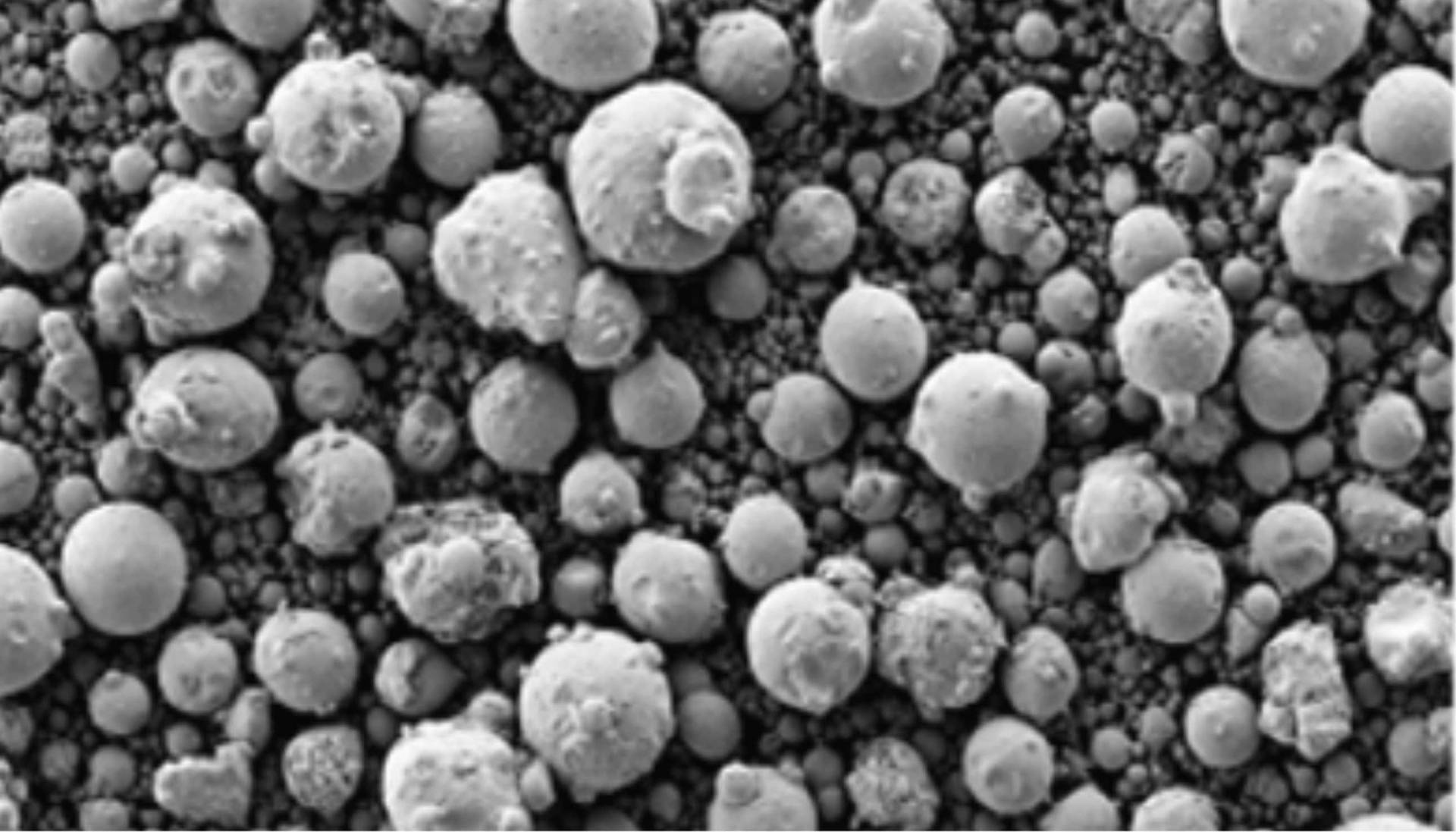
Powder with satellite formation
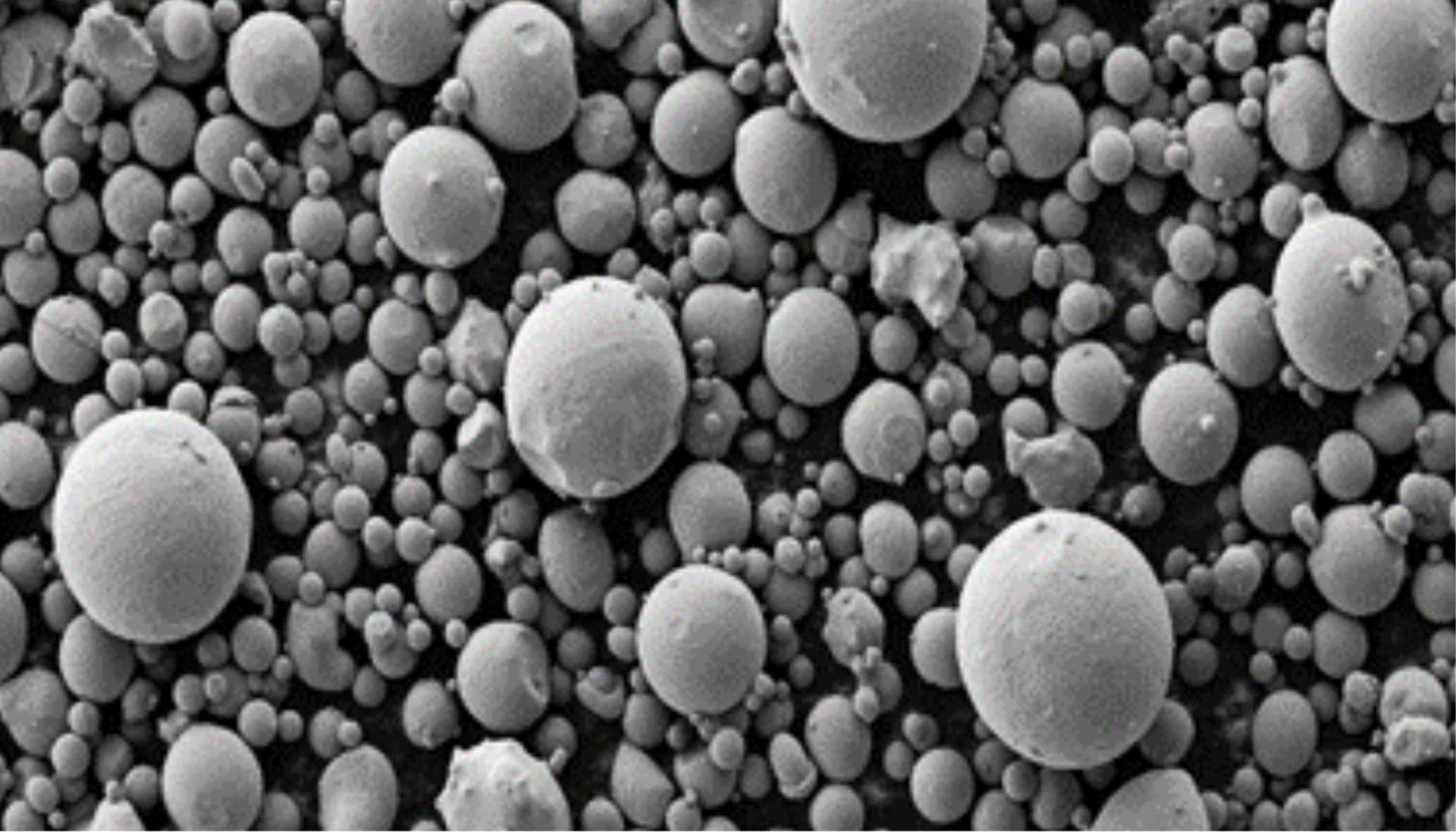
INDO-MIM Powder with no satellite formation
Below are the Particle Size Distribution of the powders,
- Metal Injection Molding: The size varies from 3~25 microns
- Micro-Metal Injection Molding: The size varies from 1~15 Microns
- Laser Powder Bed Fusion: The size varies from 15~53 Microns
- Binder-Jet: The size varies from 5~53 Microns.
Having a fleet of Laser Powder Bed Fusion (LPBF) or Selective Laser Sintering (SLS) and Binder jet production 3D printers both in India and as well as in U.S, INDO-MIM has been a widely known contract manufacturing firm providing one-stop solution to customers in delivering highly complex precision metal components. We have so far produced 200,000+ components in our Additive Manufacturing operations for customers in the medical, industrial, defense, aerospace and consumer goods market. The facility is equipped with wide range of secondary finishing operations including CNC finishing along with world-class quality assurance equipment. INDO-MIM’s investment in 3D Printing demonstrates our technical capabilities in the adaptation of newer manufacturing technologies on a production scale with the implementation of digital manufacturing in the shop floor. We remain confident of producing high-quality metal AM components with competitive cost, and material flexibility with the advantage of in-house powder production. You may reach out for more information on your metal powder requirement and AM capabilities.
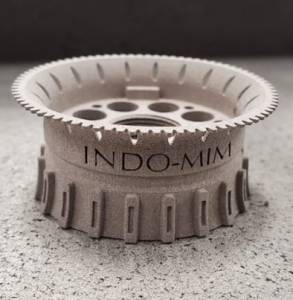