Metal Injection Molding: Precision and Innovation in Medical Applications
INDO-MIM manufactures complex shaped metal components of medical devices through Metal Injection Molding technology. We are certified with ISO 13485 and dedicated facility and ISO Class 8 cleanroom for the production of medical components.
Metal Injection Molding solution for Medical Applications.
With a strong focus on innovation and investment in cutting-edge MIM technology, we offer world-class products and services. In addition, our capabilities include advanced finish machining, heat-treating, and performance surface coatings, ensuring superior quality and performance. We also specialize in plastic injection molding and insert molding. With our expertise in supply chain management, integration, and packaging, we deliver comprehensive solutions tailored to our clients’ needs. All our operations adhere to the highest standards, taking place in our ISO Class 8 cleanroom
In the medical field, Metal Injection Molding has found various applications due to its ability to produce small, complex parts with excellent mechanical properties. Some examples of MIM components used in medical applications include:
Surgical Instruments: Metal Injection Molding is used to produce surgical instruments such as forceps, scissors, clamps, and needle holders. The process allows for the creation of intricate shapes and features required for precise surgical procedures.
Orthodontic Brackets: Injection Molding is employed in the production of orthodontic brackets used in dental instruments. MIM brackets provide excellent strength, biocompatibility, and precise fit, enhancing the effectiveness of orthodontic procedures.
Implantable Devices: MIM is utilized in the production of implantable medical devices such as orthopedic implants (e.g., bone screws, plates, and anchors), dental implants, and drug delivery systems. MIM components offer high strength, corrosion resistance, and biocompatibility required for long-term implantation.
Endoscopic Components: Metal Injection Molding is used to manufacture components for endoscopic devices, including biopsy forceps, graspers, and other tools used in minimally invasive surgeries. MIM’s capability to create complex geometries and small features is advantageous in these applications.
Surgical Staplers: MIM components are also employed in surgical staplers used in various surgical procedures. These components require high strength, precision, and resistance to sterilization processes, which can be achieved through the Metal Injection Molding process.
MIM technology offers advantages such as cost-effectiveness, design flexibility, and the ability to produce intricate metal components in large quantities. However, it’s worth noting that specific applications and materials used in medical devices must comply with applicable regulations and standards to ensure patient safety and device efficacy.
Material Selection for Medical Applications
INDO-MIM offers wide varieties of materials for medical applications. We developed more than 85+ materials based on customer requirements.
We are using Cobalt Chrome, Nickel free alloys, Stainless Steel (17-4PH, 316L, 420, 440C), Titanium Grade 5 & Grade 2, F75, Ceramics, High Temp Polymers and Liquid Silicon Rubber (LSR), etc for the production of medical devices.
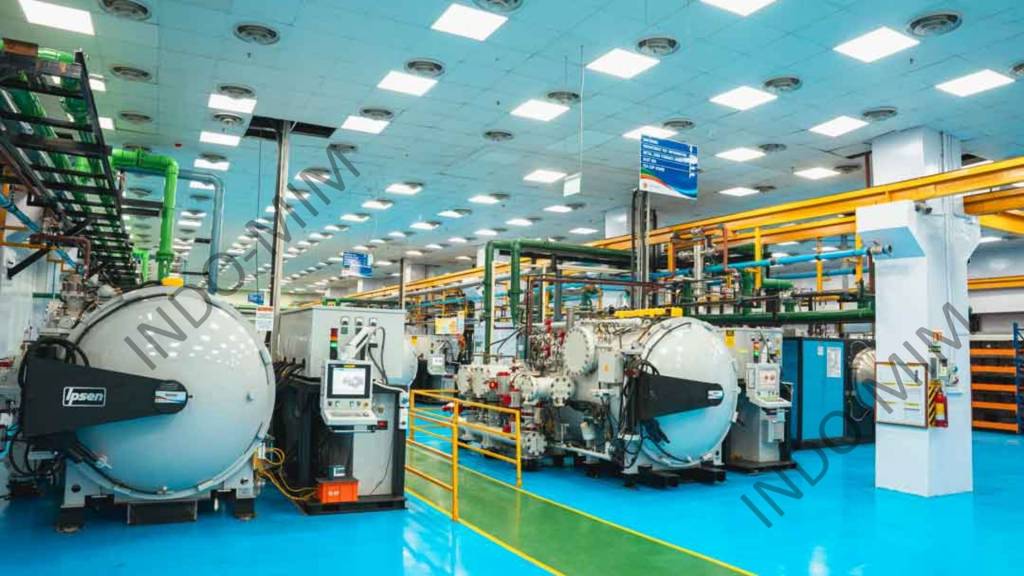
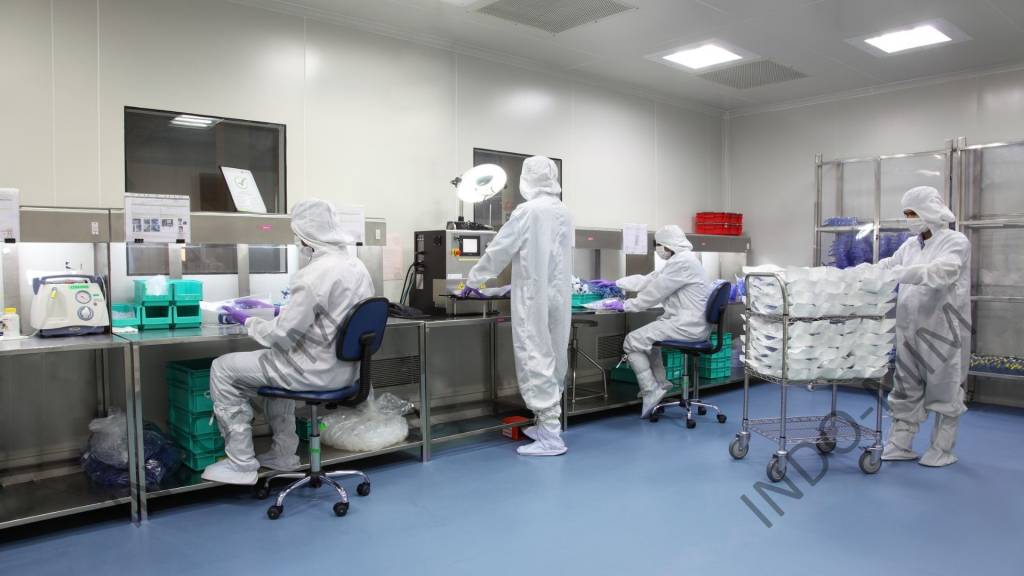
INDO-MIM Medical capabilities:
- Laser welding
- Titanium Processing
- Metal Bending (Including Tubes)
- Laser Cutting
- Plastic injection molding & Over Molding
- Silicon Injection Molding & Over Molding
- Semi / Fully automation
- Optics assembly
- Glass Bead Blasting / Tumbling
- Any Coating / Passivation
- Induction / Ultrasonic Welding
To know more about our Medical capability, click on the below link