What is 3D Printing?
It combines the design flexibility of the 3D printing components with the mechanical properties of the high-performance metal alloys to create a complex and unique shape for required application demands.
At INDO-MIM, we offer two types of 3D printing Services
- Binder Jetting
- Laser Powder Bed Fusion
What is laser Powder Bed Fusion? How does it work?
Laser powder bed fusion using a laser to scan and selectively melt the fine metal powder particles and bonding to gather and creating a part layer by layer.
The basic Cutting edge process of Laser powder bed fusion is similar to the SLM and below is the process of LPBF.
- In the beginning of the process, the build chamber is first filled with inert gas (for example argon) to minimize the oxidation of the metal powder and then it is heated to the optimal build temperature.
- A thin layer of metal powder is spread over the build platform and a high-power laser scans the cross-section of the component, melting (or fusing) the metal particles together and creating the next layer. The entire area of the model is completely scanned, so the part is built fully solid.
- When the scanning process is complete, the build platform moves downwards by one layer thickness and the recoated spreads another thin layer of metal powder. The process is repeated until the part is complete.
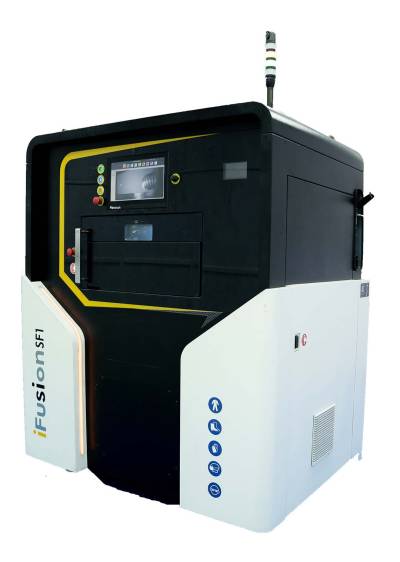
What are the common materials for LPBF 3D metal printing?
At INDO-MIM, Currently, the materials supported by us include Inconel (625, 718), Stainless Steel (316L, 410L, 17-4PH), 18Ni300, HK30, Cobalt Chrome Alloys (Co-Cr-Mo, Co-Cr-W-Mo)
Stainless steel & tool steel – High wear resistance; Great hardness. Good ductility and weldability
Cobalt-Chrome alloys –Â Excellent wear & corrosion resistance; Exceptional properties at elevated temperatures; Very high hardness; Biocompatible
Nickel superalloys (Inconel)Â – Excellent mechanical properties and strength; High corrosion resistance; Used in extreme environments
Advantages of LPBF
Powder bed fusion offers a wide range of advantages, some of which are listed below.
Design Freedom: Complex parts can be easily achieved through LPBF.
Reduced material waste – Building up the part layer by layer eliminates most of the waste associated with subtractive manufacturing technologies.
Prototype-Designers can visualize and test their ideas quickly.
Required Quantity: Small to medium batch can be produced.

Technical Specification of 3D printing-LPBF@INDO-MIM
- Build Box Size: a. 150*150*180mm b. 280*280*360mm
- Materials: Inconel, Stainless Steel, Cobolt Chrome alloy
- The surface Roughness (Ra) of the metal 3D printing is approximately is 6 – 8 μm.
- Layer Thickness: 30 to 60μ
- Angle 45 degree
- Dimensional Accuracy:± 0.1 mm
Conclusion
The world of 3D metal printing, particularly LPBF, opens up new possibilities for industries ranging from aerospace to healthcare, enabling the production of parts that were once deemed challenging or impossible. This technology continues to evolve, pushing the boundaries of design and engineering
Contact us:[email protected]
To know more about Laser Powder Bed Fusion, click below